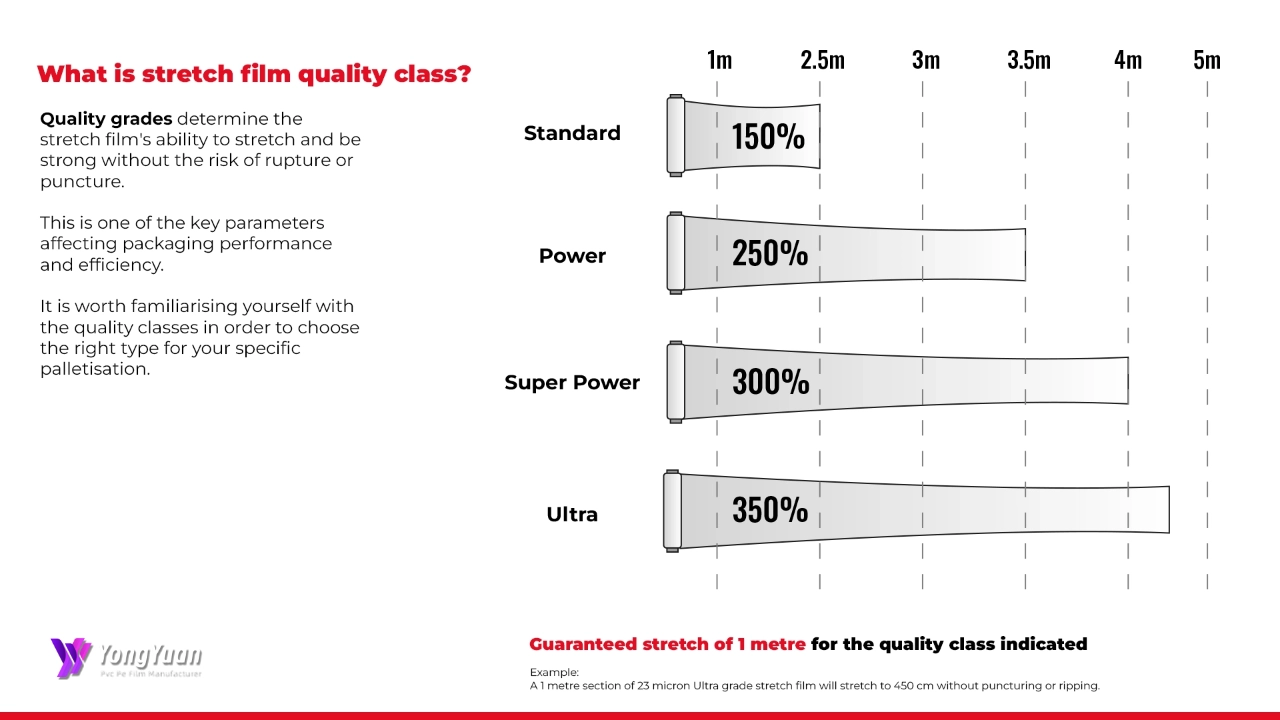
Stretch Film Quality Classes: The Key to Optimizing Packaging Efficiency and Cost Savings
1. Technical Analysis of Stretch Film: From Basics to Advanced Solutions
Stretch film, primarily made from linear low-density polyethylene (LLDPE), achieves differentiated performance through multi-layer co-extrusion technology. Core technical parameters include:
Elongation: Quantitative measure of stretch capacity (150%-370%)
Puncture Resistance: Ability to withstand sharp impacts (≥300g/μm)
Cling Force: Adhesion between film layers and cargo surfaces (0.8-1.5N/cm²)
Memory Retention: Ability to maintain consistent tension after wrapping
2. Quality Classification System: Four Tiers for Precision Application
Tier 1: Standard Grade
Performance: 150%-200% elongation, 17-25μm thickness
Applications: Manual wrapping of lightweight cartons and regularly shaped goods
Innovation: "Standard+" variants with nano-reinforced tear resistance (20% improvement)
Tier 2: Power Grade
Breakthroughs: 250%+ elongation, 300% pre-stretch ratio
Tech Highlights: Triple-layer co-extrusion (core/cling/abrasion-resistant layers), thickness reduced to 12μm
Cost Efficiency: 40% larger coverage per roll vs. Standard Grade, ideal for automated lines in food and FMCG industries
Tier 3: Super Power Grade
Elite Performance: 300%+ elongation, -50°C low-temperature resistance
Advanced Uses:
Rust-Proof Packaging: Integrated VCI (vapor corrosion inhibitor) layers for automotive parts
Cold Chain Logistics: Anti-condensation additives to block moisture ingress
Certifications: Complies with ISTA 3E, ASTM D4649 international transit standards
Tier 4: Ultra Grade
Technological Peak: Five-layer nano-co-extrusion, 370% elongation, 9μm thickness
Smart Features:
Tension-Sensing Color Markers: Visual indicators of wrap tightness
UV-Detection Layer: Color change signals film degradation
Key Users: Aerospace component manufacturers, precision instrument suppliers
3. selection Framework: A Four-Dimensional Evaluation Model
Cargo Profile
Weight Class:
Grade Load Capacity Standard ≤500kg Power 500-1,500kg Super Power 1.5-3 tons Ultra ≥3 tons Shape Complexity: High-cling films for irregular items
Equipment Compatibility
Manual Wrappers: Match 200%-250% elongation
Auto Pre-Stretch Machines: Require 300%+ elongation and precise tension control
Environmental Demands
High-Temperature Warehousing: Cross-linked films (80°C+ resistance)
Cross-Border Shipping: UV-blocking and anti-static coatings
Cost Equation
Cost per Pallet = (Film Price × Consumption) + Labor/Depreciation
Industry data shows Power Grade films reduce total costs by 18%-25%.
4. Industry Trends: Sustainability Meets Smart Innovation
Eco-Friendly Evolution
Bio-Based PE Films: Made from sugarcane ethanol, 2-year degradation cycle
Water-Soluble Films: Dissolve in 1 hour, certified by Amazon and Alibaba
IoT Integration
Embedded RFID Chips: Monitor packaging integrity in real time
Tension Analytics: AI algorithms optimize film usage and reduce waste
Custom Solutions
Branded Colors: Custom hues for enhanced brand visibility
Multi-Functional Films: Combine anti-counterfeit tags and temperature-sensitive indicators
5. Quality Assurance: Three-Step Verification Protocol
Lab Testing: Validate elongation strength and oxygen permeability via SGS reports
Field Trials:
drop Test: 1.2m free-fall x3 without film rupture
Vibration Test: ISTA-compliant 2-hour shaking with zero tension loss
Cost Audit: Compare material consumption per unit volume
Conclusion
With packaging costs accounting for 12% of total logistics expenses (per DHL research), strategic selection of stretch film grades is a critical lever for supply chain optimization. By aligning technical specifications with operational needs, businesses enhance cargo safety while building cost resilience in a volatile market. Partner with certified suppliers for tailored solutions—every roll of film can become a catalyst for profitability.