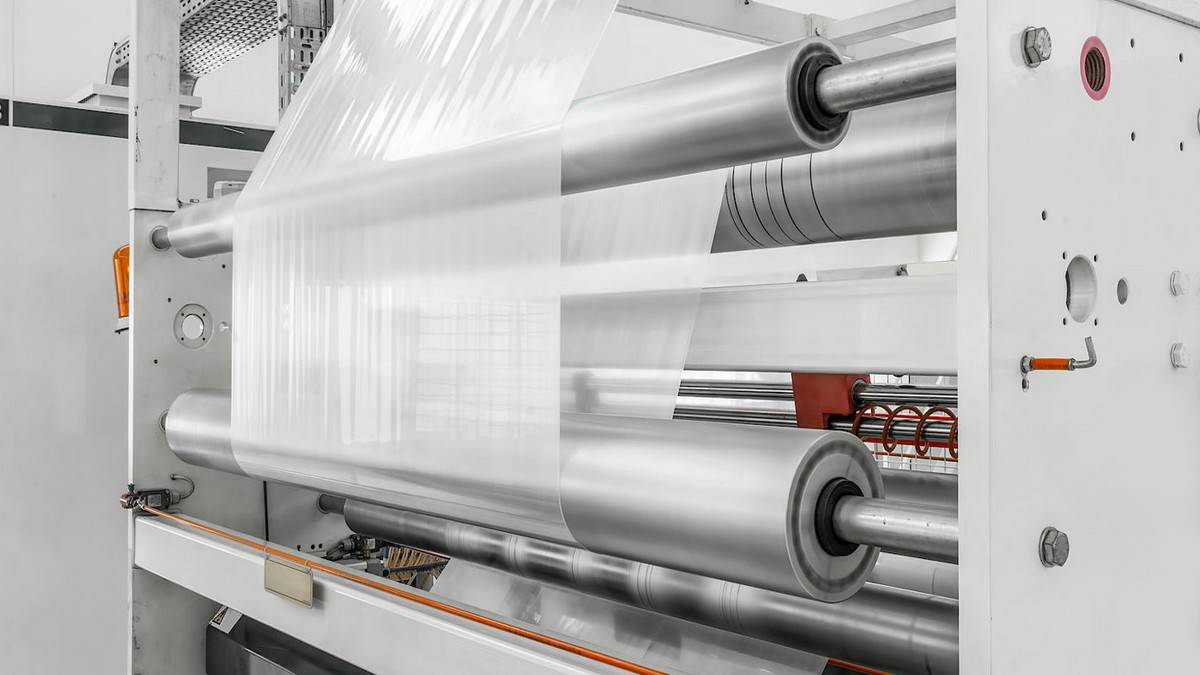
Production process and classification of polyvinyl chloride (PVC) film
Polyvinyl chloride (PVC) film can be roughly divided into two categories, one is plasticized PVC film, also known as soft PVC film (Plasticized PVC Film), and the other is unplasticized PVC film, also known as hard PVC film (Unplasticized PVC Film). Among them, hard PVC accounts for about 2/3 of the market, and soft PVC accounts for 1/3. Soft PVC is generally used for floors, ceilings and leather surfaces, but because soft PVC contains softeners (this is also the difference between soft PVC and hard PVC), it is easy to become brittle and difficult to preserve, so its scope of use is limited. Hard PVC does not contain softeners, so it has good flexibility, easy to shape, not easy to be brittle, non-toxic and pollution-free, and has a long shelf life, so it has great development and application value. The essence of PVC film is a vacuum blister film, which is used for the surface packaging of various panels, so it is also called decorative film and adhesive film, and is used in many industries such as building materials, packaging, and medicine. Among them, the building materials industry accounts for the largest proportion, which is 60%, followed by the packaging industry, and there are several other industries with small-scale applications.
The production process of PVC film is not complicated. The general production line is generally composed of a roller press, a printing machine, a back coating machine and a cutting machine. The film with a thickness of only 0.3 mm to 0.7 mm is produced mainly through the direct stirring of the roller press, the rotation of the roller and the high-temperature rolling. At the same time, the front of the film is printed with patterns by a printing machine, and a back coating is attached to the back of the film by a back coating machine. Don't underestimate this back coating, it is an important guarantee for the high-quality performance of the PVC film. The back coating is composed of special materials and is a high-energy affinity agent. It is precisely because of this back coating that the PVC film can be tightly integrated with the medium-density board or other boards, and it will not debond for ten or even fifteen years. The biggest problem of ordinary veneer films is that they cannot solve the problem of film shedding. Since the entire production process is carried out at high temperature (the temperature in the roller press reaches 220 degrees), this makes the PVC film highly light-resistant and fire-resistant, ensuring the high quality of the PVC film.